工厂或配送中心场内的布局,似乎只是在建设过程中要考虑的问题。如果运作不顺畅,就抱怨设计不合理;物流操作效率低,就责怪管理层当时只看生产需求而不考虑物流实际……
事实上,场内布局从来就是一个系统工程,它既需要物流的输入,也有输出给物流,通过输入与输出的持续运行,才能让布局越来越合理,越来越高效。
全局平面
很多员工都不了解所在工厂或DC的整体布局,只清楚自己日常工作的区域,更别提外来人员了。
在这样的环境下,经常会有物流司机等外部人员来提送货时两眼发黑,进了场就不知道往哪里走、如何办单、哪个地方停车排队、行驶路线是怎样才合规……要是场内布局比较复杂的话,可能发生的事情就不仅限于效率低下了,甚至有发生安全事故的隐患。
因此,在入场的门口、主要片区的进出口,应当设置包含物流区域在内的全局平面图,并清晰地展示给所有人,让人知道自己现在哪个地方,要去的区域位于什么方位,哪些地方是不能去的……
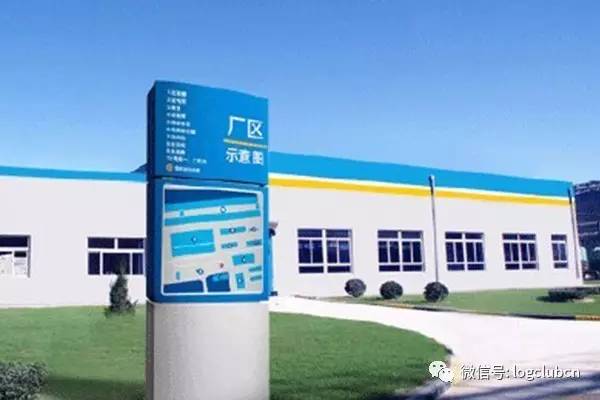
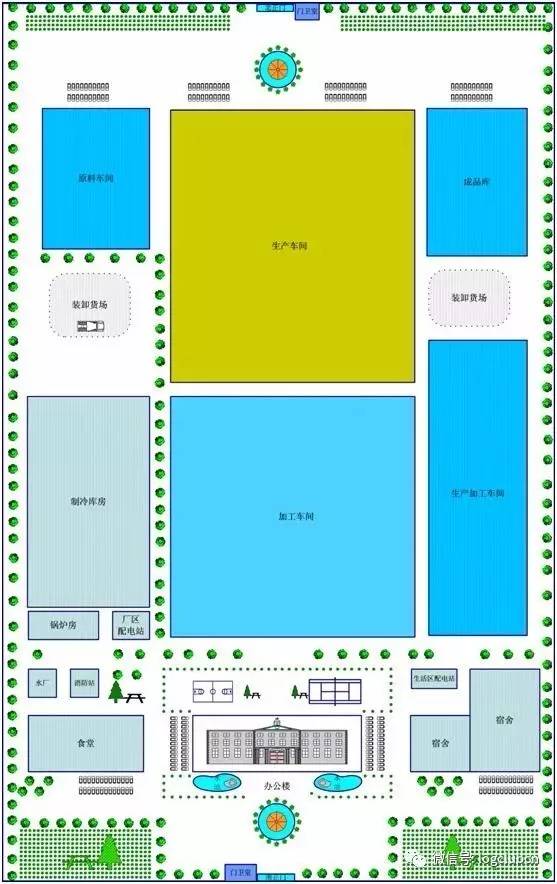
运行路线
知道自己在哪里,也知道要往哪里去,还得清楚如何走过去。
很多现有的工厂和DC因场地限制,不能够有足够宽的大马路让车辆肆意行驶,甚至连人车分离都有一定难度,于是作为整个场内作业范围最广、车流最大的物流部门,应该协助行政、安全等部门,规划好车流、人流的路线。
尽量减少车辆交汇、调头、与人相遇的机会,增加单行、环形、人车分离的设计。
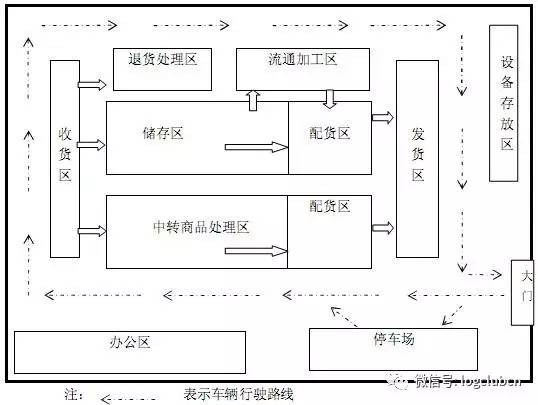
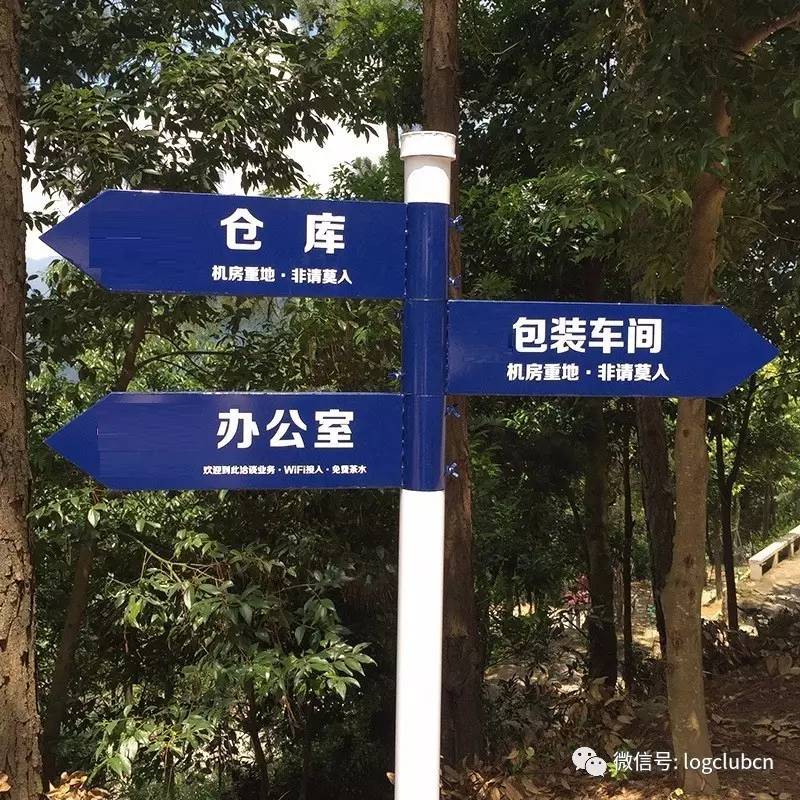
设置好后,以简洁直观的形式,如上图的指示牌在相应的路口给人以明确指引,减少走错倒车或调头情况的发生。
各区要求
有了全盘的分区布局,明确了每个区到目的区的行走线路,接下来就是确保每个区域的人员行为符合相应的规范,最重要的是安全标准。
比如到材料仓卸车的外来司机,进厂要求限速5公里、下车时必须穿反光背心、给车轮垫止动块等要求;在成品库的外协车队调度员,要求穿劳保鞋、穿有反光条的工作服、戴安全帽等……
每个区域的标准要充分考虑受众和场景,譬如对司机的要求就张贴在从他进厂开始到停车休息室的范围,不能跟仓库其他人员的要求混在一起,让所有人都不知道哪些要求是针对自己的,哪些要求是针对他人的,因而也就无从遵守了。
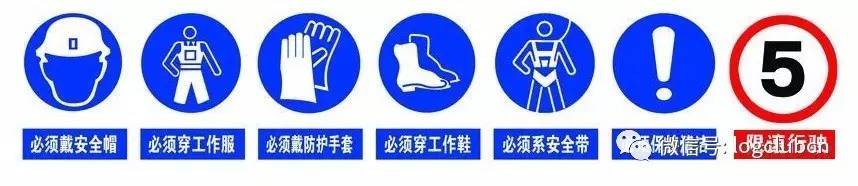
总之,场内布局不是一张死板的施工图,而是需要不断优化的运行图,为入场人员清晰展示全盘布局,指定行走路线,明确各运作区域的安全规定并落实执行,这样才能让场内的物流、人流按照期望的方式活动。
分功能区
每次新建仓库时,各工厂(DC)的高层都会很重视,由专业的人甚至请外部咨询公司来制定仓库布局。
专业人士会从产品特性、数量、运行路径、物流提供的服务、时间安排等数据去分析流程和各运作要素之间的行为关系,然后再根据仓库内的可用空间确定空间关系,结合要素组织的原则和技术限制、安全及一些外部因素,来统筹制定几个专业化的方案供筛选。
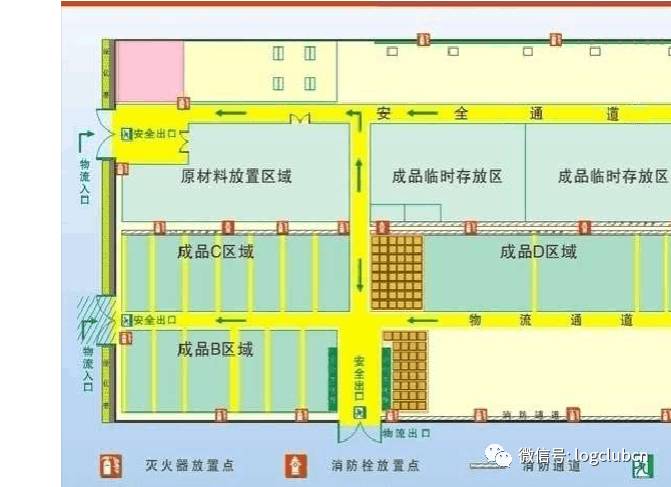
我这里要重点说的不是具体如何产生这些专业的方案,而是强调一个非常重要但容易被忽略的输入——现场运作人员的反馈。很多当初设想非常完美的方案,到了实际运作时就会暴露各种问题:
功能区划分不合理,要么空间不够而要占用其他功能区,要么浪费空间被其他产品占用;想要的功能区(如零头区)位置不理想,操作(如拆零)得绕远路;相应的设施(如货架)不好用,跟实际产品性质相差太远(如驶入式货架进深过多,蜂窝损失严重)……
因此,要让分功能区的专业方案能扎实落地,必须在方案调研环节充分听取现场仓库运作人员的意见,而不只是相信数据;也要在方案筛选环节邀请运作人员代表参与讨论,他们的现场经验和直观感受如果能够得到足够的重视,方案结合实际进行调整,落地的时候就能发挥更大的效用。
分区运作
方案里绘制出来的分区布局,只是起步而已,能够得到执行才算有意义的布局管理。仓库管理人员应该定期对比绘制的布局方案(最好在仓库现场有张贴)与实际运作的布局,从运作中去发现布局的匹配性问题从而进行改善。
例如当初设计时把空托盘的堆放区画在角落的地方,但实际运作一段时间后发现叉车司机在忙不过来时喜欢把托盘堆在靠近出货区的位置,于是就从这个差异出发,梳理流程看是否从运作角度考虑,在近出货区的位置腾出几个板位当做空托盘的周转区。
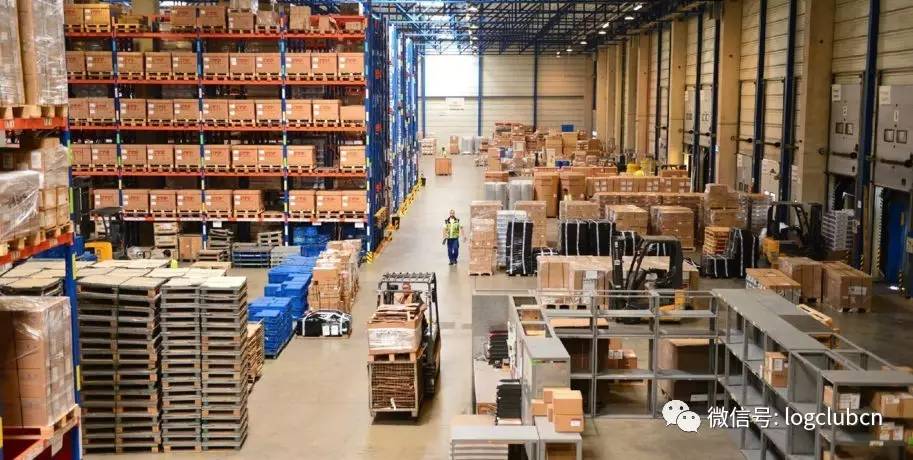
布局完成后不应该机械地要求仓库运作人员百分之百执行,而是得通过反复对比差异,优化运作,如果发现确实是布局不够合理,那就修改布局。
越来越接地气的新布局能让运作人员越来越有自觉性去遵守,而非知道一套,操作另一套,那样不切实际的布局方案,再专业也是虚的。
明显标识
绘制的仓库布局在现场得到执行后,为了让每个功能区更具可视化,不至于让新手迷惑,也能让管理人员甚至高层来检查时可以直观地看到仓库管理成果、发现具体问题,则现场必须做好明显的分区标识。

没做多少标识的仓库靠员工的经验进行管理,经验再丰富都会出错,或者出了错不容易暴露出来;做了明显标识的仓库依靠的则是标准管理的方法,也会出错但很容易发现运作的不足之处,能够得到快速的改正。
总之,仓库布局不是只靠专业人员用专业工具就能画出来的,要充分考虑运作人员的意见并作为重要的输入,才能输出一个相对合理的布局方案,在执行中进行回顾,不断改善布局使其最优化,让仓库管理从依赖人变成依靠标准。
产品数据分析
作业区内并非每一平方米的面积都是同等价值的,里面需要作业的各种产品也不应被一视同仁。
以仓库为例,入库到出库行驶距离最短的区域就属于“黄金铺位”,假如仓库进和出都在同一侧的门口,那么离门半径最小的库位就是最金贵的;离进出口半径最大的库位就属“偏远地区”,所以仓库如果按地段来收租的话,每个区域的租金理应是不同价位的。
虽然通常我们不会这样拉开差价去计费,但布局时应当考虑与不同周转区“身份”匹配的产品,分析出产品作业量最大的产品应当放在最大周转区,周转最小(慢动)的产品放在远的地方,从而令整体、长期作业的行驶总距离最小化。
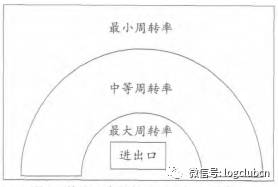
以上只是其中一种方式(进出口在同一侧),还有一侧进另一侧出,或者U型等不同的作业方式,得具体情况具体分析(综合业务量、收发货频率、周转快慢等因素),让进和出距离最短的“黄金地段”留给A类产品。
作业区设施特性
定好了作业区内的库位等级,接下来就要考虑各等级库位的设施如何与相应的产品匹配起来。每种设施具有不同的特性,要根据产品的特点来选择和设计、调整不同的设施。
例如同样是货架,驶入式货架适用于存放大批量的单品,而横梁式货架就更适合小批量的多品种。以下图为例,在仓库“黄金地段”安装的全是驶入式货架,A类产品(红白相间的单品)存储在里面可以充分利用空间,总体设计方向是对的。但考虑得不够周全。
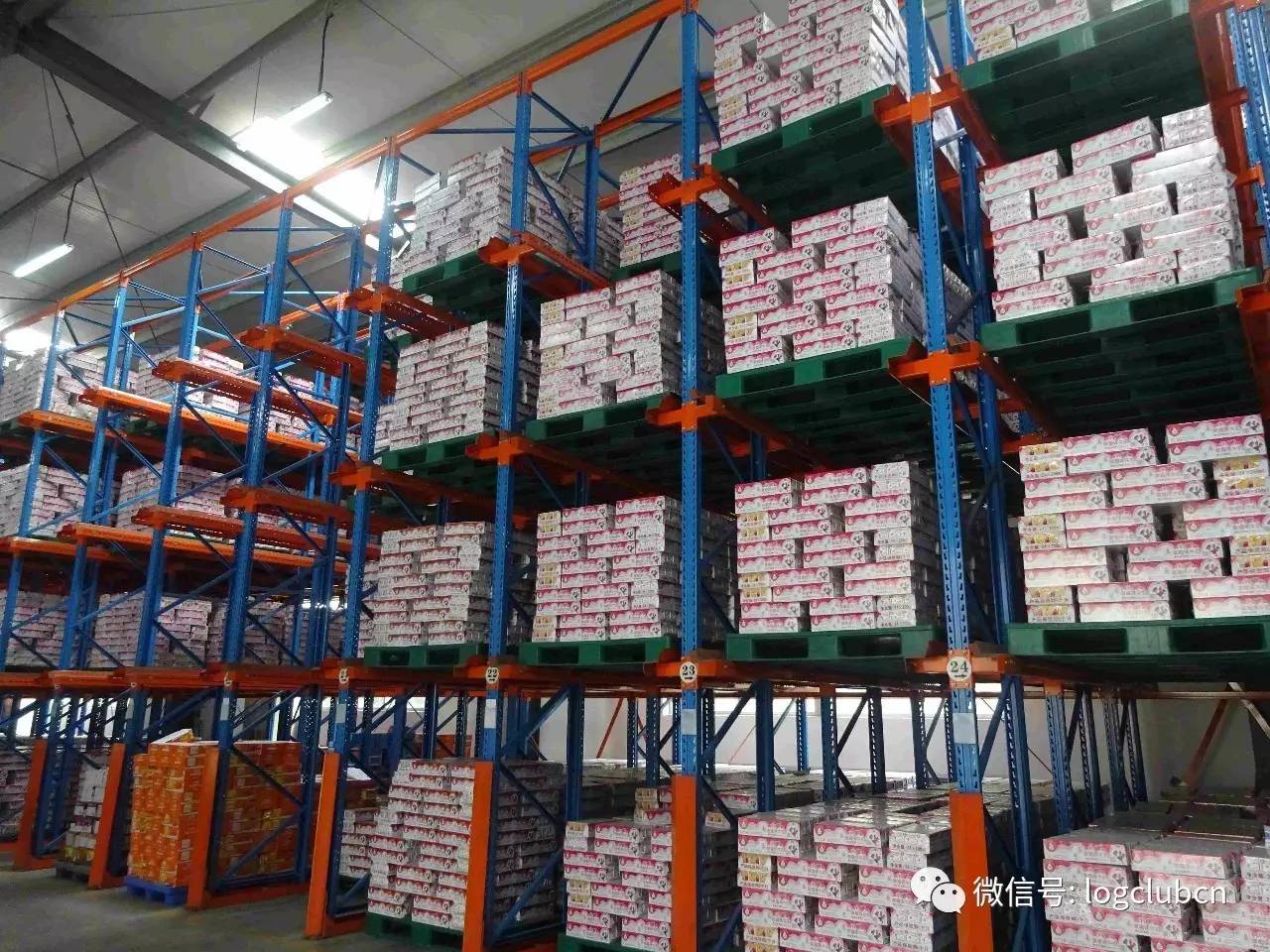
从上图可以看出,左下角有一个橙黄色的品种也存储在驶入式货架中,但其数量少,所以同一个库位内大部分的托位空间都浪费了,蜂窝损失严重,其实用横梁式货架会更合适。
而存储周转量最大货物的驶入式货架,也未充分考虑A类产品的特性,比如高度。所有库存产品中,最高的品种有1.55米(托盘底到货物顶),于是全部货架都按每层1.7米来设计(预留叉车升降空间)。
而全部A类产品每托只有1.3米高,于是就造成了大量的空间浪费。若有充分考虑产品特性的布局,可能会让A类产品区的货架层高下降,增加一层储位,从而进一步提升“黄金位置”的存储能力。
订单运作回顾
从产品特性、操作流程、空间活动及关联度进行分析;对作业区面积、分品种周转量、不同储位的设施进行匹配以外,检验布局效率的高低还得通过实际订单的运行。
因为通常每个作业区的订单量不是持续平均的,要考虑每月、每周至每日的波峰波谷,让各个时间段的作业都具有高效性和和灵活性。
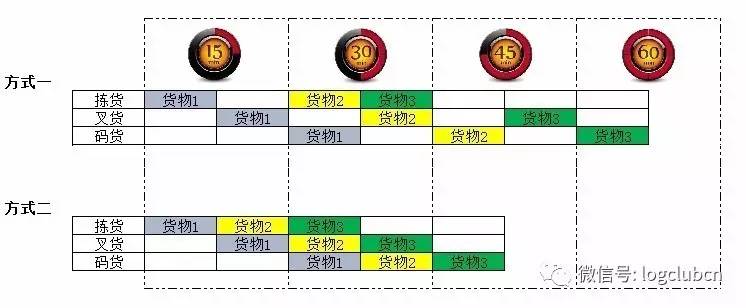
以上图片是非红在讲解仓库管理模块时,用来描述作业次序和装卸资源的匹配,以节省时间的例子,其实与现场布局也有关系。
譬如原来的备货区只有50托的空间[方式一],某个时段要出库的三种货物分别需要50托、30托和20托来缓冲,当拣货人员把货物1在15分内全部备好在缓存区时,50托货全部已经占用,他要等叉货司机将货叉到货车上给搬运工码货后,才能继续把货物2的30托和货物3的20托备到缓存区,让后续作业环节进行。
若是经过充分的订单作业数据分析,发现有必要将备货区从50托增加到80托的库位,那订单的运作状况就更加顺畅了[方式二]:
拣货人员备好货物1后,叉车司机在50托的库位里操作货物1却不影响拣货人员在剩余30托的空间里放入货物2,当搬运工在货车上堆码货1时,叉车司机在30托的空间里将货物2叉出,而此时原来的50托库位已经空出,能让拣货人员连续拣选放入货物3、货物4……持续不断,方能高效。
总之,现场布局不是划分出一块块就足够的,要通过产品特性、操作流程、空间活动及关联度进行分析;对作业区面积、分品种周转量、不同储位的设施进行匹配,再用实际波动的订单不断进行检验和调整,才能让布局适应高效的作业需求。
来源:非红物流 作者:非红